Imagine a factory churning out widgets, day in and day out. Every widget is supposed to be identical – the same size, weight, and quality. But, in the real world, things are never perfect. Some widgets might be slightly too large, others slightly too small, and some might have flaws. How do we ensure that these variations stay within acceptable limits and that we consistently produce high-quality products?
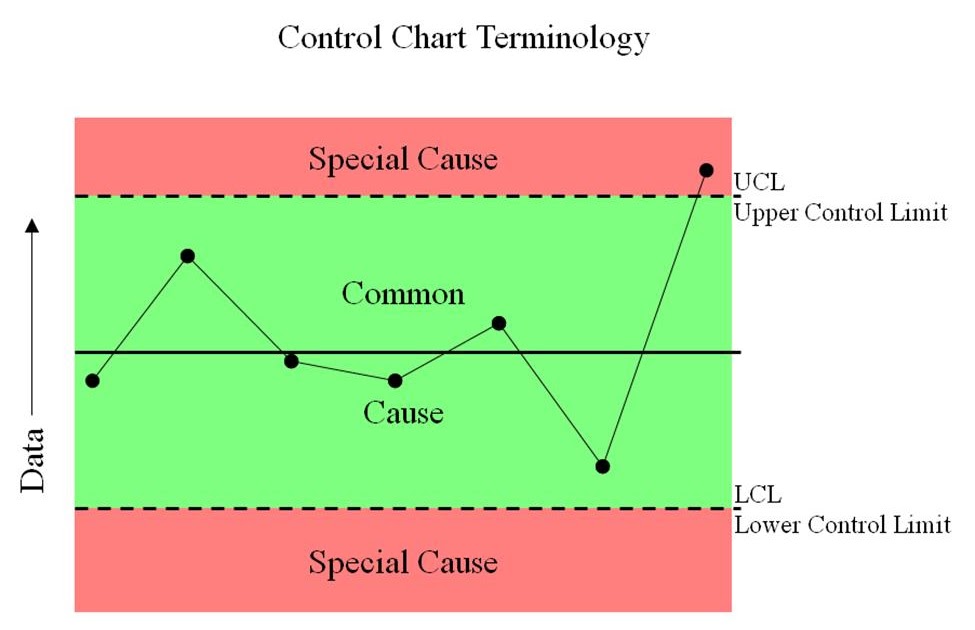
Image: testsoftinc.blogspot.com
Enter Statistical Process Control (SPC). This powerful tool, using statistical methods, helps businesses monitor and manage their processes to maintain consistency and quality. It’s not about simply measuring and recording data; it’s about using that data to identify and correct problems before they snowball into major issues.
The Need for Control
Before delving into the specifics of SPC, let’s examine why we need it in the first place. Think of a manufacturing process like a river. It flows constantly, and its course is influenced by numerous factors. These factors, known as “variables,” can be anything from the temperature of the furnace to the skill of the worker.
Every variable introduces a degree of variation into the process. Some variations are natural and expected, like the slight differences in the size of individual widgets. However, other variations can signal problems, like a sudden change in temperature causing a batch of widgets to be significantly smaller than usual.
Without proper control, these variations can accumulate, leading to a decline in product quality, increased waste, and ultimately, unhappy customers. This is where SPC comes in.
The Foundation of SPC: Understanding Variation
The heart of SPC lies in understanding and controlling variation. As we’ve discussed, variation is inherent in any process. The key is to differentiate between “common cause” variation and “special cause” variation.
Common Cause Variation
Common cause variation is the inherent, predictable variation that’s always present in a process. Think of the slight differences in the size of our widgets – this is common cause variation. It’s a natural part of the process and can be attributed to the complex interplay of many factors.
Common cause variation is usually manageable and controlled through the normal operating procedures of the process.

Image: www.presentationeze.com
Special Cause Variation
Special cause variation, on the other hand, is unusual and unpredictable. It’s like a rock thrown into our river, disrupting the normal flow. This variation usually signals a problem that needs to be addressed. It could be a faulty machine, a worker error, or a change in the raw materials.
Special cause variation is often easily identified and corrected by analyzing the process data. For example, a sudden spike in the number of defective widgets might indicate a problem with a machine that needs to be serviced.
The Power of Control Charts
SPC uses a variety of tools to analyze and control variation, but the most vital one is the control chart. Imagine a control chart as a visual representation of your process over time. It plots a series of data points, usually measurements taken from the product or process, along with upper and lower control limits. These limits define the range of acceptable variation.
Interpreting Control Charts
Control charts help us understand the behavior of our process. If all the data points fall within the control limits, it suggests that the process is stable and only common cause variation is present. This means the process is predictable and under control.
However, if a data point falls outside the control limits, it signals a special cause variation, indicating a problem or a change in the process. This requires immediate attention and investigation.
Control charts are incredibly valuable for businesses because they provide a visual and objective way to assess the health of a process. They empower us to see trends, anticipate potential issues, and take proactive steps to maintain quality.
Benefits of Statistical Process Control
By implementing SPC, businesses reap numerous benefits, which can lead to significant improvements in efficiency, quality, and profitability. Here are some of the key advantages:
1. Improved Quality
The primary goal of SPC is to ensure consistent product quality. By understanding and controlling variation, companies can minimize defects and produce products that meet customer expectations.
2. Reduced Waste
SPC helps to detect and eliminate waste, whether it’s in the form of defective products, unnecessary rework, or inefficient processes. This leads to cost savings and increased productivity.
3. Increased Efficiency
SPC empowers companies to identify and streamline inefficient processes, optimize resource allocation, and reduce bottlenecks. This results in smoother operations and faster production cycles.
4. Better Decision-Making
SPC provides data-driven insights that allow management to make informed decisions about process improvements, resource allocation, and problem-solving.
5. Customer Satisfaction
By delivering consistently high-quality products, businesses using SPC can cultivate satisfied customers, boost brand loyalty, and enhance their reputation in the market.
Applications of Statistical Process Control
The applications of SPC are vast, extending far beyond manufacturing. Here are just a few examples:
Manufacturing
SPC is a cornerstone of quality management in manufacturing. It’s used to monitor and control everything from the weight of a chocolate bar to the precision of an engine part.
Healthcare
SPC is used in healthcare to improve the accuracy of diagnostic tests, monitor patient outcomes, and ensure the consistency of medical procedures.
Finance
Financial institutions use SPC to monitor market trends, identify risks, and measure the performance of investment portfolios.
Software Development
SPC is used to track the number of defects in software applications, identify areas for improvement, and ensure the reliability of software products.
The Future of Statistical Process Control
SPC is constantly evolving. New technologies, such as artificial intelligence and predictive analytics, are being integrated into SPC methodologies. These advancements allow for more sophisticated data analysis, real-time monitoring, and proactive problem-solving.
The future of SPC is bright. As businesses continue to strive for excellence, SPC will remain an essential tool for achieving quality, efficiency, and customer satisfaction.
What Is The Rationale And Basis For Statistical Process Control
Conclusion
Statistical Process Control is a powerful tool for businesses that want to maintain consistency and quality in their operations. By understanding the principles of variation, utilizing control charts, and embracing the benefits of SPC, companies can unlock a world of opportunities for improvement and growth. Whether you’re a seasoned manufacturing executive or a budding entrepreneur, understanding the rationale and basis of SPC will equip you with the knowledge to navigate the ever-changing landscape of business and deliver exceptional results.