Have you ever been frustrated by inconsistent welds? Maybe your wire feed was uneven, creating gaps or weak spots in your project. That’s where a reliable wire drive assembly becomes your welding superhero! And today, we’re going to explore the Lincoln SP 100 wire drive assembly, a robust and efficient component that sets the standard for precise welding in your workshop.
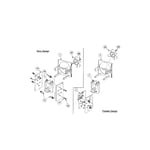
Image: www.searspartsdirect.com
The Lincoln SP 100 wire drive assembly is a core component in many welding machines, and it plays a critical role in providing accurate and consistent wire feed. Its effectiveness is crucial for achieving those beautiful, strong welds that make your projects stand out. We’re going to dive deep into the world of the Lincoln SP 100 wire drive assembly, exploring its anatomy, benefits, and how you can optimize its performance for your welding needs.
Understanding the Lincoln SP 100 Wire Drive Assembly: A Journey Inside
The Lincoln SP 100 wire drive assembly is carefully engineered to deliver precise wire feed regulation. It’s a vital component that directly influences the quality of your welds. The assembly itself is a masterpiece of mechanics and electronics, featuring:
-
The Drive Motor: The heart of the assembly, this powerful motor is responsible for smoothly feeding the welding wire onto the contact tip. By ensuring consistent wire feed speed, it eliminates those frustrating variations that can impact weld quality.
-
The Gearbox: A finely tuned gearbox meticulously transforms motor rotation into linear wire movement. It’s like a miniature symphony of gears, each playing its part in achieving precise, controlled wire feed.
-
The Wire Feed Rollers: These rollers, strategically positioned within the assembly, grip the welding wire. They are the key to preventing wire slippage during the welding process, ensuring that the wire is fed at a consistent pace.
-
The Drive Rollers: These rollers are crucial for pushing the wire towards the contact tip. They provide the precise control necessary for smooth and continuous wire feed.
-
The Wire Feed Control: This intelligent system allows you to adjust the wire feed speed based on your welding application. This is where your control comes in; you can fine-tune the wire feed to achieve optimal weld performance.
Benefits of the Lincoln SP 100 Wire Drive Assembly: Unlocking Your Welding Potential
The Lincoln SP 100 wire drive assembly is more than just a mechanical component; it’s your partner in achieving professional-quality welds. Here’s how it enhances your welding experience:
-
Consistent Wire Feed: This is the foundation of successful welding! The Lincoln SP 100 wire drive assembly guarantees consistent wire feed speed, regardless of your welding project. No more inconsistent welds!
-
Enhanced Weld Quality: By eliminating wire feed variations, the assembly paves the way for superior weld quality. You’ll achieve strong, even welds that stand the test of time.
-
Increased Productivity: With a reliable wire drive assembly, your welding process becomes more efficient. You spend less time troubleshooting and more time creating stunning projects.
-
Versatility: The assembly is compatible with a wide range of welding materials, making it an invaluable tool for various projects. Whether you’re working with steel, aluminum, or other metals, the Lincoln SP 100 wire drive assembly can handle your welding needs.
Maintenance and Troubleshooting: Keeping Your Wire Drive Assembly in Top Shape
Just like any precision instrument, the Lincoln SP 100 wire drive assembly benefits from regular maintenance for optimal performance. Here are a few tips:
-
Regular Cleaning: Brush away any debris or wire shavings from the assembly. This helps prevent wear and tear and ensures smooth wire feed.
-
Lubrication: Apply a light oil to the gears and drive rollers, following the manufacturer’s guidelines. Proper lubrication keeps moving parts running smoothly and efficiently.
-
Wire Feed Adjustments: Always check and adjust your wire feed speed before starting any welding project. Ensure the correct setting is selected for the wire size and welding application.
Common Troubleshooting Steps
-
Wire Feed Speed: If you are experiencing inconsistent welds, start by checking your wire feed speed. Ensure it’s set appropriately for your current welding project.
-
Drive Rollers: Inspect the drive rollers for wear and tear. If they are worn or damaged, replace them immediately.
-
Wire Feed Guide Tube: Make sure the wire feed guide tube is free of obstructions. A clogged tube can create problems with wire feed.
-
Contact Tip: Check the contact tip for excessive wear. If it’s worn down, replace it to ensure proper electrical contact and wire feed.

Image: techschems.com
Expert Insights and Actionable Tips
-
Choose the Right Wire: Select the appropriate welding wire for your project. Choosing the wrong wire can lead to inconsistent welds and problems with wire feed.
-
Listen to Your Machine: Pay attention to any unusual sounds coming from the wire drive assembly. A grinding or squealing noise can indicate a problem. Address any unusual sounds promptly to avoid further damage.
-
Don’t Overlook the Basics: Proper grounding and connection methods are essential for welding safety and success. Pay close attention to these critical steps.
Lincoln Sp 100 Wire Drive Assembly
Conclusion: A Tool for Every Welder
The Lincoln SP 100 wire drive assembly is a crucial component in boosting your welding skills and achieving professional-quality results. Its consistent wire feed, enhanced weld quality, and versatility make it a valuable asset for both novice and experienced welders. Now that you have a deeper understanding of this remarkable component, your welding journey will be smoother than ever, with flawless projects to showcase your skills. Keep these tips and best practices in mind, and you’ll enjoy the benefits of this essential welding component for years to come!